Abstract: HJS has recently launched its latest developed high-speed and high-precision die bonding machine.
This new product is the HJS high-speed, high-precision, fully automatic die bonding machine, with a mounting accuracy of 1.5 microns and dual station collaborative work, improving efficiency by 50%. The equipment is the latest research and development of this year, specifically tailored for high-precision and high reliability COC/COS eutectic packaging applications such as optical communication, high-power commercial lasers, and LiDAR. While maintaining high precision and flexibility, it greatly improves production capacity and efficiency by using dual station parallel work. Currently, this new product was officially launched on the market in September this year.
“The new die bonding machine has made significant performance improvements on the original product, including new improvements in the sports platform, visual effects, addition of pulse heating dual eutectic system, and unique MV application software. At the same time, it supports multi process production, providing customers with more stable surface mounting accuracy and faster surface mounting speed. HJS continuously strives to provide customers with domestically produced crystal solidification equipment with high-tech and high-precision requirements.” The technical leader of HJS stated.
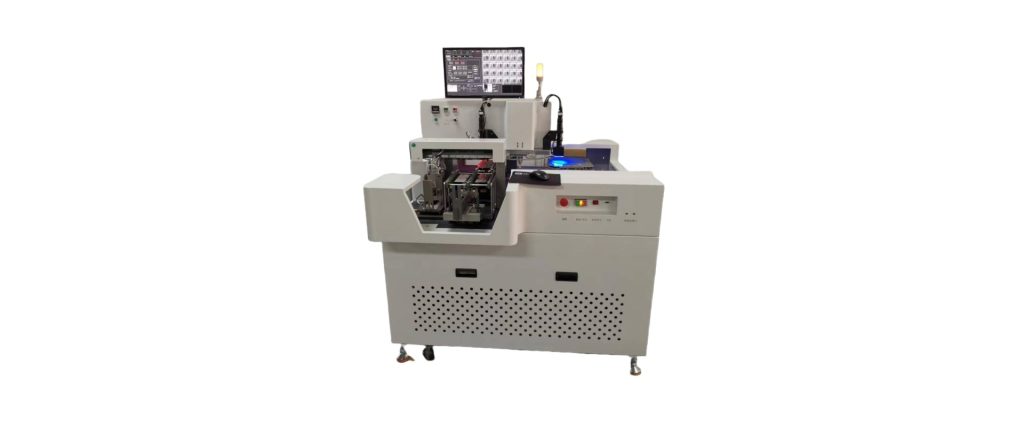
Equipment features:
1. Sports platform
Using high-grade marble as the base; The Y-axis (gantry axis) is a dual drive form, installed on a marble base; The X-axis (gantry axis) is installed on the Y-axis; Z-axis is installed on the X-axis; The Theta axis (rotation axis) is installed on the Z-axis.
Advanced design concepts and the application of high-precision components provide smoother and more precise capabilities for motion control platforms. It can accurately control position, speed, and torque under complex conditions.
The main system uses a linear motor with zero locking force, no iron core, and active cooling for the X and Y axes, paired with a high-resolution linear encoder to ensure high-speed and precise motion. To ensure motion accuracy, the heat source is cooled by gas in the design. High precision encoders can achieve fast, precise, and closed-loop positioning. Linear motors can provide higher speeds (acceleration, deceleration, and speed) while accurately controlling the motion position to ensure overall smooth motion.
2. Visual system
Configure high and low magnification up and down cameras with sub micron level visual accuracy. Advanced visual systems can quickly detect and orient chips within the device’s large working area. Using edge recognition or graphic recognition technology to locate the center and direction of the component, and to locate the alignment base point of the component.
Edge recognition and pattern recognition are used to locate the center, edge, or other key features of a chip. Quick orientation function, global and local visual alignment can be used for alignment of embedded substrates and features, enabling fast and accurate processing of complex components.
3. Lighting system
The camera is equipped with a white collimation lighting system and a circular lighting system (red, green, and blue), with adjustable brightness.
The intensity of the annular and coaxial light of each camera can be programmed and controlled. Optimized lighting conditions can be set for chip recognition and alignment. The application of multi-color background light can optimize the imaging of low contrast components. Red, green, and blue programmable light sources are more powerful in handling difficult surfaces.
4. Pulse heating twin eutectic system
Dual pulse heating system, high-speed temperature rise and fall, programmable temperature curve, and adjustable speed. The eutectic stage matches various parameters required by the eutectic process through programming control. Meanwhile, programmable mechanical scraping can be used to optimize welding quality. The design configuration of two eutectic workbenches significantly improves production efficiency.
5. Substrate transfer system
High precision substrate loading and unloading, dedicated suction nozzle, no need for time-consuming replacement of suction nozzle. Unique substrate and chip dual grasping design, integrated into automated production. In conjunction with the dual eutectic system, the substrate nozzle grabs the substrate from the waffle box to the eutectic stage, and then grabs the welded chip substrate back to the material box from another eutectic stage, seamlessly switching and eliminating the tedious nozzle replacement process, greatly improving production efficiency.
6. Application software
Flexible process platform, programmable and configurable process applications, supporting multiple process flows.
A beautiful and intuitive graphical user interface simplifies settings and production process programming. The component is simple and easy to learn, and includes all process procedures, allowing for data manipulation and offline programming. Advanced visual tools can perform the most challenging visual processing of substrate and chip materials. Scanning QR codes to select production programs frees up operators, reduces error rates, and maximizes production efficiency. The entire production process is automatically archived, with traceable historical records, making process optimization more convenient. Statistics on the use of tools and consumables such as suction nozzles and ejector pins, with prior notice of replacement, can avoid significant waste of components. Real time fault notification simplifies maintenance costs.
7. Optional modules such as flip table, blue film system, automatic loading and unloading system, and software and hardware customization services are available.
About HJS
HJS is a high-tech enterprise specializing in the research and production of high-precision and complex process chip packaging equipment. Over the past four years, the company has continuously made comprehensive efforts in new product research and development, application implementation, and social responsibility, achieving leapfrog development. HJS’s product performance is comparable to international first-class competitors, with short lead times, good service, obvious cost advantages, and a secure supply chain. We sincerely strengthen cooperation with our customers to help strengthen the domestic industrial chain and create a win-win story.
Key words:
Wafer bonding | Chip handling equipment | Die attach process | Die bonder machine | Die sorting technology | Flip chip bonding | Chip handling equipment | die sorter | semiconductor die sorter | automated die sorter | wafer die sorter | die sorting equipment | die bonding and sorting | high speed die sorter | wafer mapping | die bonder | semiconductor die bonder | automated die bonder | die bonding equipment | die bonder machine | high precision die bonder | die attach | semiconductor die attach | automated die attach | die attach process | eutectic die bonder | epoxy die bonder | die sorting machine | automated die sorting machine | high speed die sorting machine | precision die sorting machine | flip chip die sorting | MEMS die bonding | sintering bonding | IGBT bonding equipment | EEL COB Epoxy bonding | Multi dies and different angle bonding | FMCW Mixed packaging | multi chip COC eutectic | Heating tip flip chip bonding | CoS/Bar eutectic | Single COS to Box Eutectic | PA device bonding | Multi channel Lens passive bonding | Bare die to tape and reel machine | wafer to tape and reel | wafer to waffle | wafer to tray | atomic force microscope